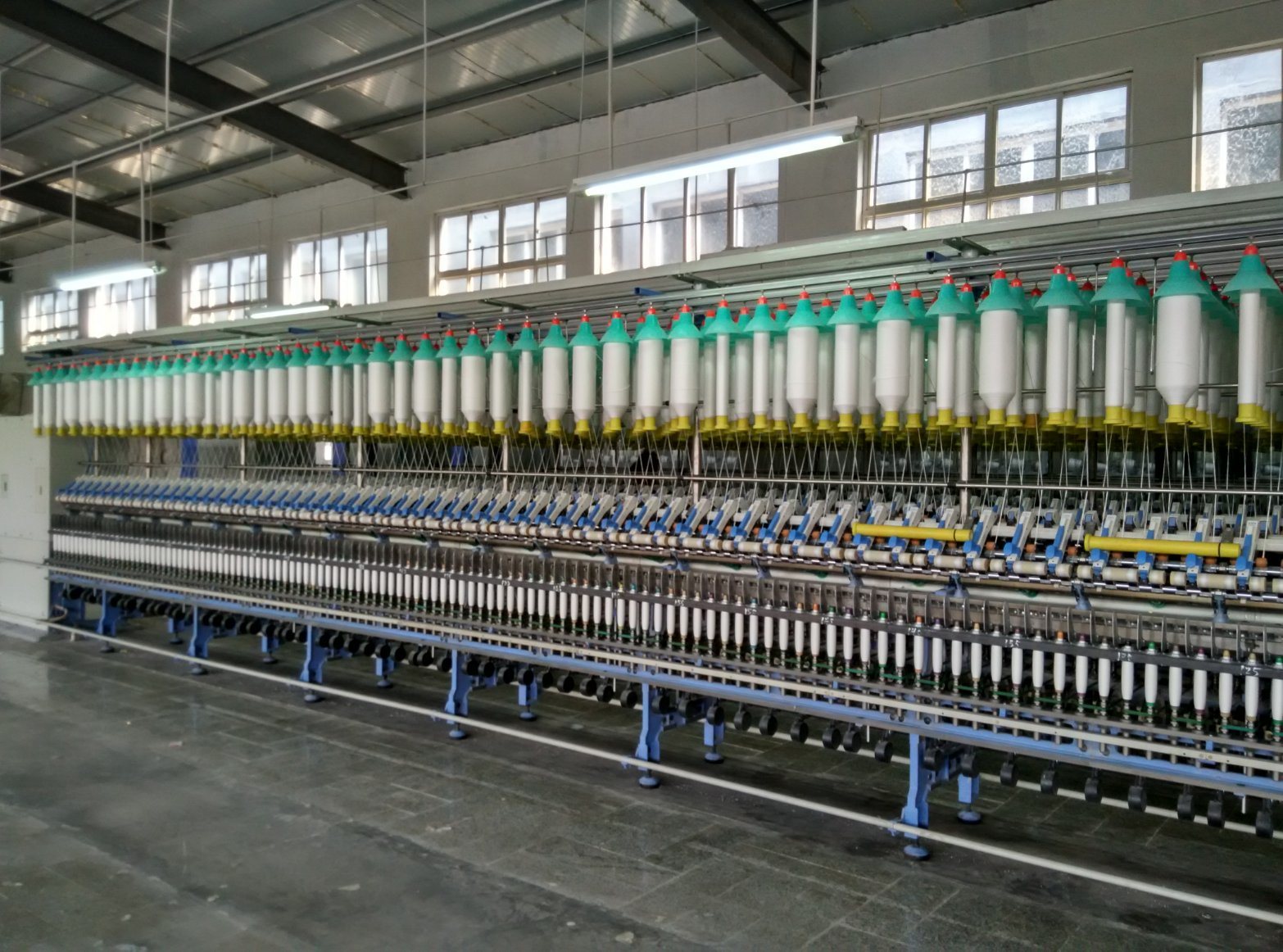
About Spinning
Khalis Fiber’s spinning process for converting recycled Poly-Ethylene Terephthalate (PET) bottles into fiber yarn is a finely tuned and environmentally responsible procedure that reflects their commitment to sustainability. Here’s a glimpse into this essential stage:
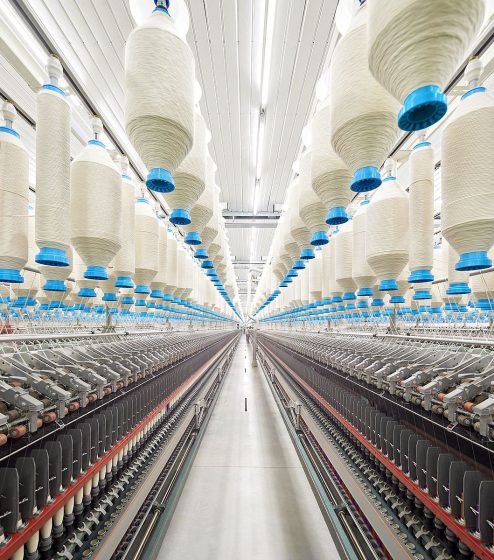
After collecting and cleaning PET bottles, the plastic is transformed into small resin pellets. These pellets serve as the raw material for the spinning process. The PET resin pellets are heated to a molten state and then extruded through spinnerets, which are specialized nozzles with tiny holes. This extrusion process forms continuous, fine filaments of molten plastic. As the filaments emerge from the spinnerets, they are rapidly cooled and solidify. This step is crucial to maintain the desired fiber properties and structure. The solidified filaments are drawn and stretched to align the polymer chains, increasing the strength and uniformity of the resulting yarn. This stretching process can be controlled to achieve different yarn thicknesses and characteristics. The stretched filaments are wound onto spools to create a continuous strand of fiber yarn, ready for further processing and application in various industries.
Our spinning process ensures that the resulting fiber yarn exhibits high-quality properties, making it suitable for diverse applications while simultaneously contributing to the reduction of plastic waste and the promotion of sustainable practices.
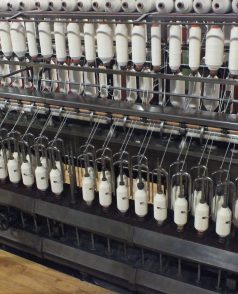